Hammer crusher is one of the commonly used equipment in the sand production line and the crushing production line. It is widely used in the crushing of iron ore, sandstone, gypsum, blast furnace slag, coal gangue, lump coal and other medium hard ore. There are many types of hammers for compound crushers. The following four types of hammers are commonly used.
1.Medium manganese steel hammer:
Medium manganese steel hammer head (manganese content is 5%-9%), the actual service life of this hammer head is more than 50% higher than ZGMn13, and a relatively good use effect has been achieved. When the as-cast manganese steel hammerhead breaks the albite, its service life is increased by more than 60% compared with ZGM13. At the same time, the biggest advantage of the as-cast manganese steel hammer is that it has magnetic properties, and the iron scraps in the ore can be removed by magnetic separation to ensure the sintering quality of the ceramic products.
2. High manganese steel hammer:
High manganese steel is a traditional material of hammerhead. After years of use, it is found that the high manganese steel hammerhead is not wear-resistant and has a short service life. The hammerhead of broken limestone can generally work for 2-3 months. Under some working conditions, it is used. Less than a week. The reason why the high-force steel hammer is not wear-resistant is that the wear of the hammer head is mainly based on scouring wear. Secondly, the impact force of the hammer head of the hammer crusher during operation is not large, so that the high-manganese steel The hammerhead work hardening effect is not significant. The greater the weight of the hammer, the greater the impact force, and the more significant the strengthening effect.
Therefore, as a material for large hammers, reinforced high manganese steel is still an alternative material. Adding Cr-reinforced high-manganese steel hammerhead, when crushing iron ore, the service life of hammerhead is 50% higher than that of ordinary high-manganese steel, and ultra-high manganese steel with manganese content of 17%-19% can also be used. At the same time, the elements such as Cr and Mo are added to improve the properties such as yield strength and initial hardness, and good results are obtained in actual production.
3. Low alloy steel hammer:
Low alloy steel hammer has a high service life, but its manufacturing process is complicated. It is strictly forbidden for the iron block to enter the crusher during the colleague. It is generally required to have a secondary iron suction device at the front end of the feed. To this end, in recent years, a variety of multi-component low-alloy steel hammerheads have been developed, the matrix structure of which is martensite, bainite or martensite plus bainite composite structure. Under the same working conditions, its service life is at least doubled than that of high manganese steel hammers.
4. high chromium cast iron composite hammer:
High-chromium cast iron composite hammer is a wear-resistant material with excellent anti-wear performance, but its toughness is low, brittle fracture is easy to occur. In order to make the high-chromium cast iron hammer safely run, people have developed a composite hammer, that is, high-chromium casting. In the head of high-manganese steel or low-alloy steel hammer head, or the hammer head does not use high-chromium cast iron, the hammer handle part is made of carbon steel, which combines the two to make the hammer head have high hardness and high wear resistance. The hammer handle has high toughness, and the advantages of the two materials are fully utilized to overcome the disadvantages of the single material to meet the performance requirements.
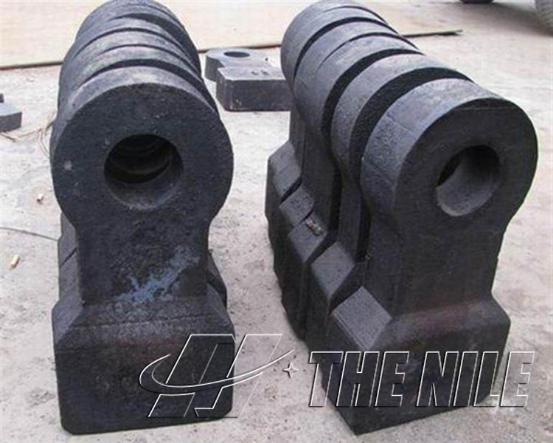
The larger the size of the crusher, the heavier the weight of the hammer, and the greater the blockiness of the material to be crushed. Therefore, the impact load on the hammer is also greater. For this reason, when selecting the material, first consider the hardness to be improved under the premise of ensuring the toughness of the hammer. The blockiness and hardness of the broken material. The higher the hardness of the material, the higher the hardness requirement for the material of the hammerhead and the greater the blockiness of the material, the higher the toughness requirement.