As a part of sand aggregate, sand is generally divided into natural sand and artificial sand. Rock particles with particle size less than 4.75mm formed by natural conditions (mainly rock weathering) are called natural sand. Artificial sand, also known as machine-made sand, refers to rock particles with nominal particle size less than 4.75mm made by mechanical crushing and screening.
Natural sand has the advantages of smooth shape, hard texture and low mining cost. It is an ideal building raw material. High quality natural sand can be obtained by properly screening and washing the collected sand and gravel. However, the over exploitation of natural sand will have a serious impact on the environment and ecosystem. Therefore, the exploitation of river sand has been banned in China.
Artificial sand has the advantages of convenient single gradation control of rock type, rough aggregate surface and good bonding effect with cement, and can be processed and mined all year round. The disadvantage is that the mining cost is much higher than that of natural sand. Machine made sand is divided into coarse sand, medium sand and fine sand according to fineness modulus. Its particle size is generally divided into 2.36 ~ 4.75mm, 1.18 ~ 2.36mm, 0.6 ~ 1.18mm, 0.3-0.6mm and 0.15-0.3mm.
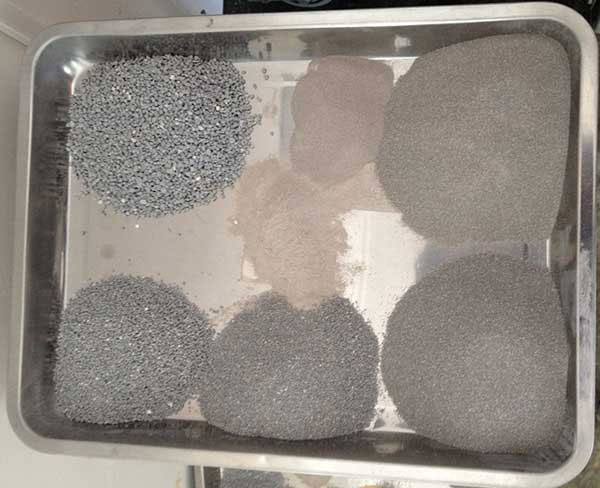
The sand production line process can be divided into two types: dry sand production line and wet sand production line.
Wet sand production generally uses a sand washer to clean the screened sand to remove stone powder or mud. If the mud content in the raw materials is relatively high, a roller stone washer is often equipped before screening. The aggregate produced by wet sand making is relatively clean, and there is no dust pollution in the air due to water cleaning. However, in the process of washing, it will also wash away some fine particles less than 0.6mm while removing soil, impurities and stone powder less than 0.075mm, On the one hand, it will cause poor grading of machine-made sand particles, larger fineness modulus and lower concrete strength. On the other hand, it reduces the capacity and wastes resources. At the same time, it is also easy to cause water pollution and affect the ecological balance.
The dry sand making process is later than the wet process, which is further introduced on the basis of the traditional wet sand making production line. The main series products of dry sand production line are composed of hopper, vibrating feeder, belt conveyor, sand maker, vibrating screen, elevator, high-efficiency powder concentrator and silo group. It does not need water to remove mud and powder in the process of sand production. Dry production gets rid of environmental restrictions, saves water resources and reduces water pollution. At the same time, it increases powder selection and dust collection equipment.
Common equipments:
The wheel sand washing machine has the advantages of simple structure, adjustable screen, lower failure rate than the screw sand washing machine, little loss of fine sand and stone powder, good gradation of washed machine-made sand, easy control of fineness modulus and stable product quality.
Spiral sand washer has the characteristics of low energy consumption, high processing capacity and low sand return rate. However, compared with wheel sand washing machine, it has the disadvantages of large water consumption, large loss of medium and fine sand and stone powder, poor gradation of washed machine-made sand, difficult control of fineness modulus and large fluctuation of product quality.
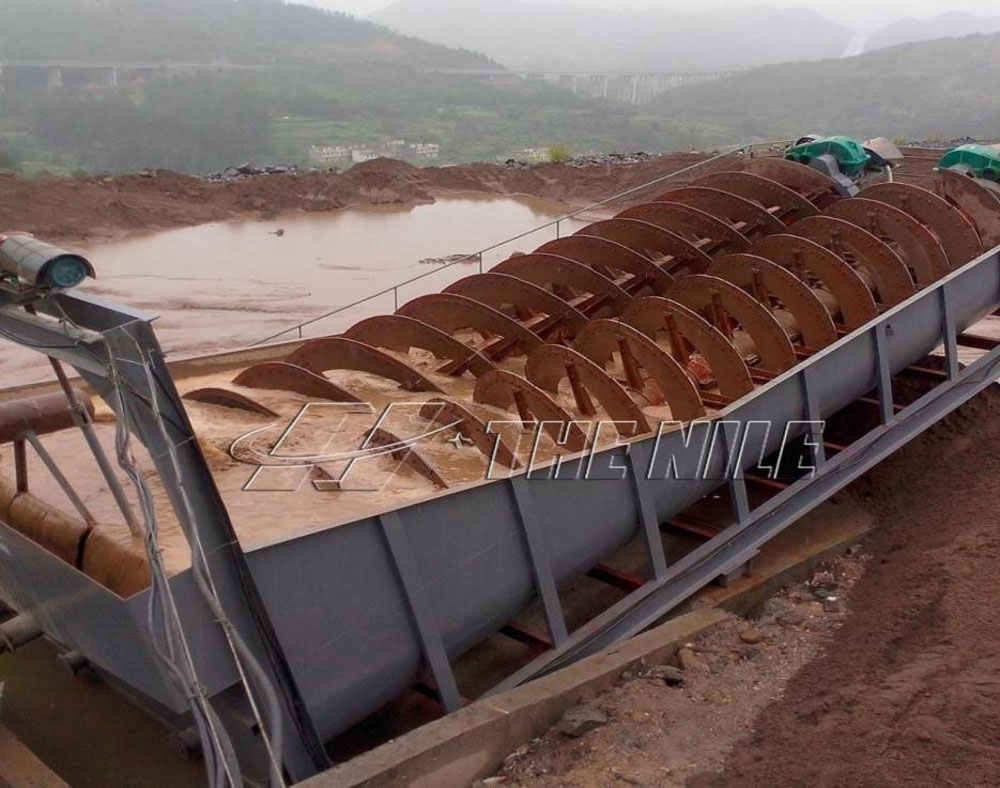
Powder concentrator is often used to remove unqualified stone powder in dry sand production. Its main working principle is: After entering the powder concentrator, the materials fall onto the spreader. Under the high-speed rotation of the spreader, the materials are scattered around by the inertial centrifugal force and lifted upward by the updraft generated by the blades of the spreader. The finer particles float upward, the coarser materials fall along the cylinder wall and are hit by the lower cage shape rotor. The fine powder returns upward to the circulating air for classification again, and the coarse powder is discharged from the inner cone through the trickle device.
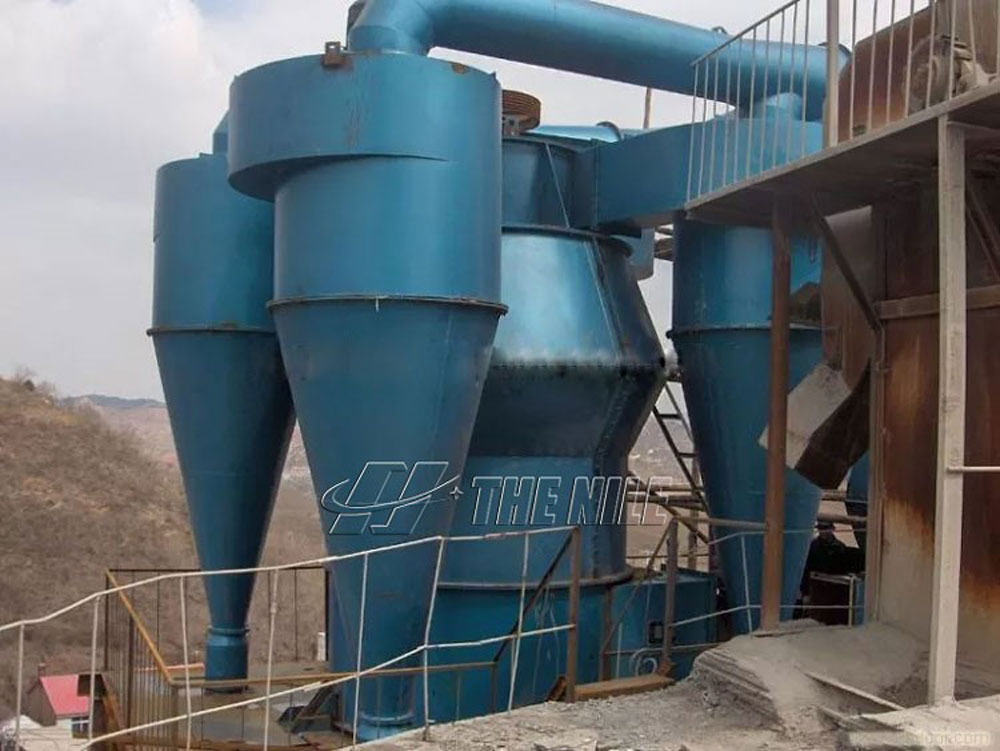

The main function of the fine sand recycling machine is to clean, dehydrate and grade the sand and stone, which can well recover a large amount of fine sand lost by the sand washing machine in the traditional sand making industry. The pump transports the sand water mixture to the whirlcone and the fine sand after centrifugal classification and concentration is supplied to the vibrating screen through the sand setting nozzle. After dehydration by the vibrating screen, the fine particles are effectively separated from water. A small amount of fine sand and mud will be sent back to the water storage tank and when the liquid level is too high, they are discharged through the discharge port.