The wet pan mill mainly uses to stir, roll, and crush the raw materials. When the wet pan mill is working, the material is fed from the middle of the roller, and it is pressed under the roller under the thrust of the scraper or its own centrifugal force. After being subjected to multiple rollings, the particles meeting the size requirements leaked out of the sieve holes around the rollers, and the coarse particles were returned to the rollers to be crushed. Wet pan mill is suitable for crushing materials below medium hardness, or for mixing materials.
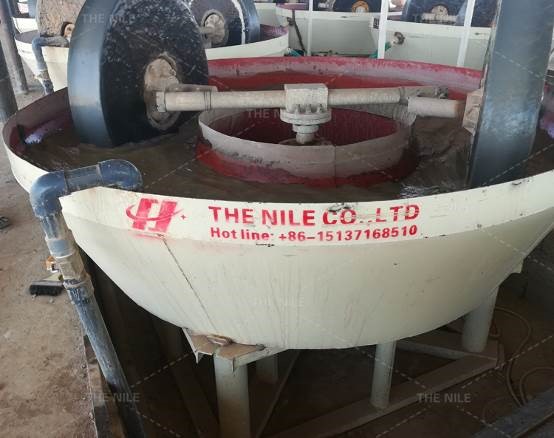
When the wet pan mill is installed, the vertical shaft must be rolled vertically. During installation, the vertical shaft can be hoisted first, and the roller can be moved so that the center hole of the roller is aligned with the vertical shaft, and then the vertical shaft is dropped into the hole vertically. The two rollers must be of equal weight and equal rotation radius. A concrete fence should be built around the wet pan mill. Stone bars are arranged in the fence to prevent the rollers from throwing out and ensure safe operation. After the installation is completed, after checking the tightening of the screws in each part, you can test run. If the operation is normal and there is no abnormal noise, it can be put into production. If there is any abnormal noise, stop the operation immediately for inspection.
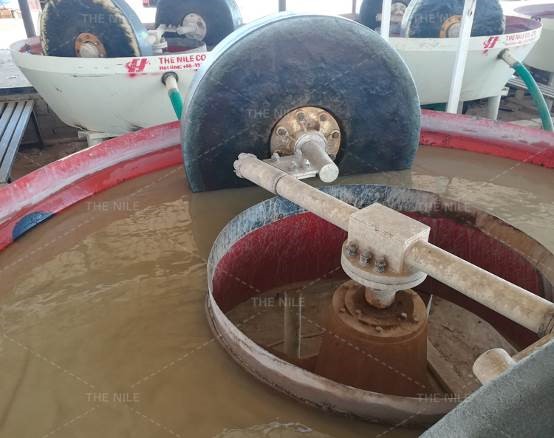
When the wet pan mill is working, in addition to crushing the material, it is also accompanied by milling. The wider the wheel, the greater the relative sliding phenomenon and the greater the milling effect. Therefore, when using a wet pan mill to crush different materials, the choice of wheel width should be specifically analyzed. The wheel width is generally between 300mm. If there is a large grinding effect (such as crushing silica), the roller can be wider; if it is mainly crushed, the wheel width can be smaller.
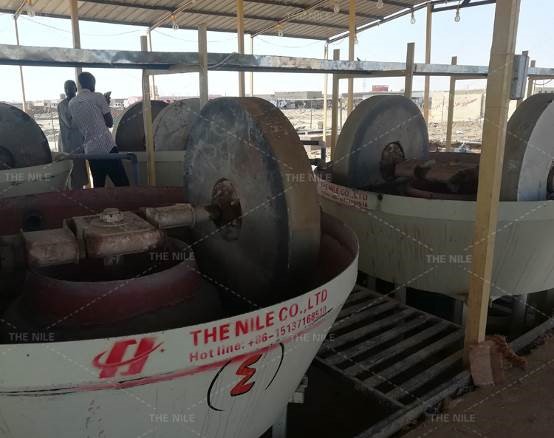
The stone wheels wear quickly and usually need to be replaced in two months. A pair of stone wheels must be replaced at the same time. Before replacement, prepare the square sleeve in advance, go down to the groove of the new stone wheel, and fill it with cement. Pay attention to the position of the stone wheel when installing. When the stone wheel is too close to the center of the pan, the water material should not be washed out and the material is discharged slowly. Therefore, it is repeatedly rolled and the material is too thin, which may cause suspended materials. Straight out, the pellets are coarse and can not meet the crushing requirements. Due to the limitation of the installation height of the equipment, the stone wheel and the roller cannot be replaced at the same time. During operation, start with an empty car, and then feed after normal operation; when stopping, shut down the feeding equipment 15 minutes in advance, and stop after the ground material is unloaded.